Yes, carbon fiber parts can be CNC machined, but the process requires special considerations due to the unique properties of carbon fiber composites. Carbon fiber is a hard, abrasive material that can wear down cutting tools quickly and generate fine dust that can be hazardous if not properly managed. Yixing is a leading carbon fiber manufacturer in China who can provides carbon fiber material and do secondary fabrication like CNC machining.
Below are key points to consider when CNC machining carbon fiber parts:
1. Challenges of CNC Machining Carbon Fiber
Tool Wear: Carbon fiber is highly abrasive, which can rapidly wear down cutting tools.
Delamination: Improper machining can cause layers of the composite to separate.
Dust Generation: Carbon fiber dust is hazardous and requires proper extraction and filtration.
Heat Build-Up: Excessive heat can damage the resin matrix or cause tool failure.
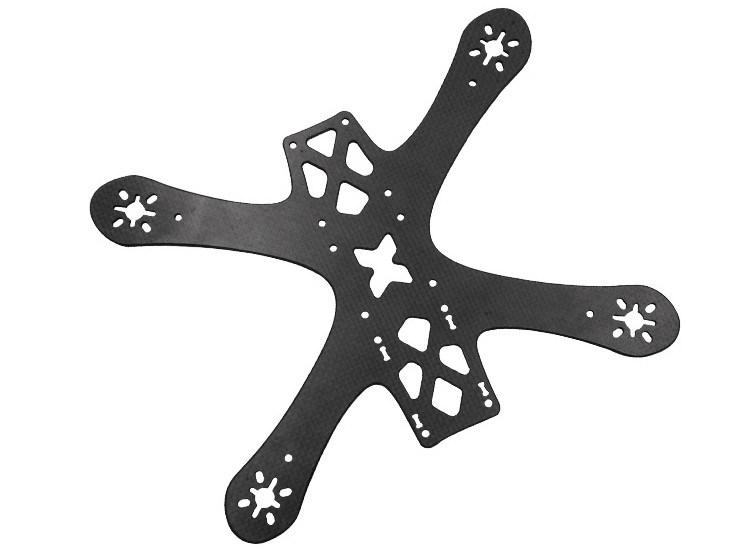
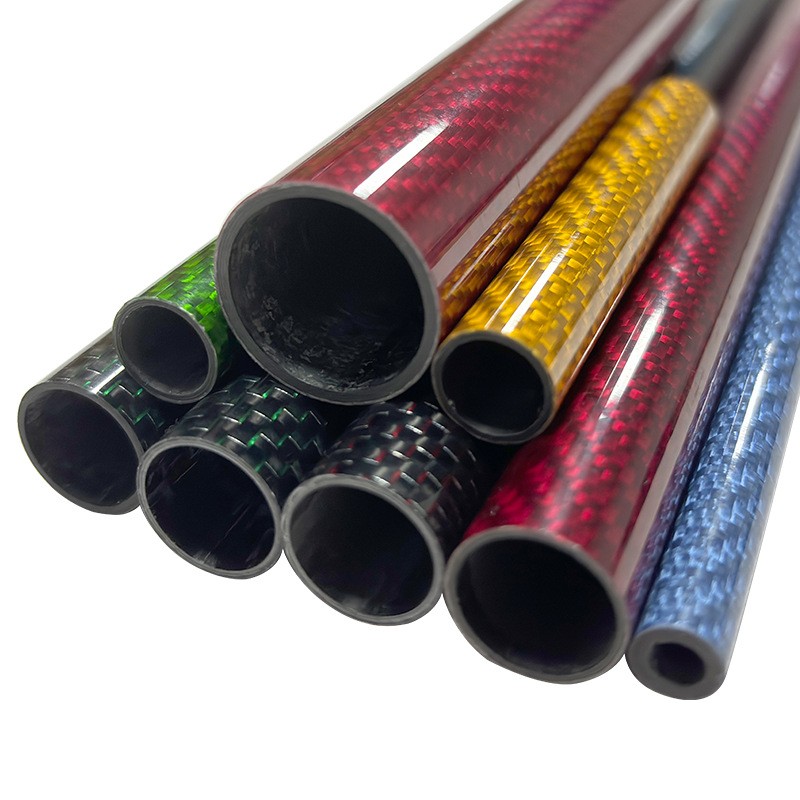
2. CNC Machining Techniques for Carbon Fiber
Tool Selection:
Use polycrystalline diamond (PCD) or carbide tools for their hardness and wear resistance.
Avoid high-speed steel (HSS) tools, as they wear out too quickly.
Cutting Parameters:
Use high spindle speeds and low feed rates to minimize heat and tool wear.
Ensure proper chip evacuation to prevent re-cutting of material.
Coolant and Lubrication:
Use air blast or mist cooling to reduce heat and remove dust.
Avoid excessive coolant, as it can weaken the resin matrix.
Fixturing:
Use vacuum fixtures or soft jaws to securely hold the part without damaging it.
3. Machining Processes
Milling:
Suitable for creating complex shapes, pockets, and contours.
Use climb milling to reduce delamination and improve surface finish.
Drilling:
Use sharp, specialized drills to prevent fraying or delamination at hole edges.
Consider peck drilling to clear chips and reduce heat.
Turning:
Used for cylindrical parts, but less common due to the layered structure of carbon fiber.
Cutting:
Use diamond-coated blades for clean cuts without fraying.
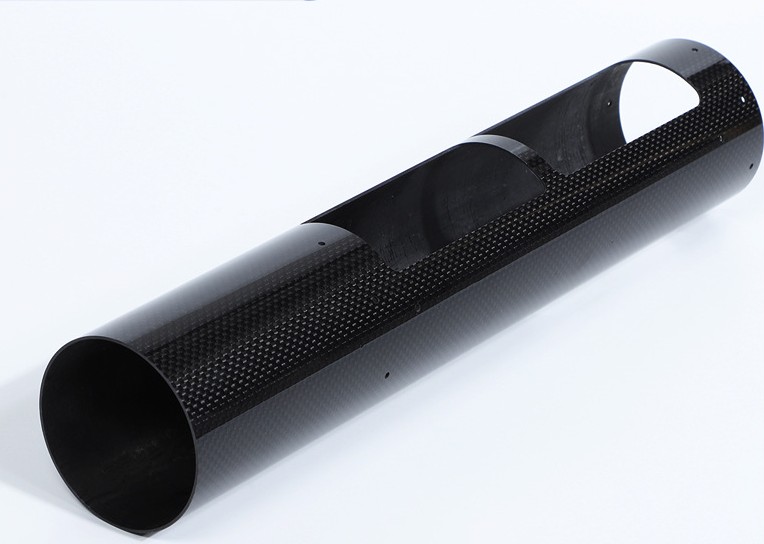
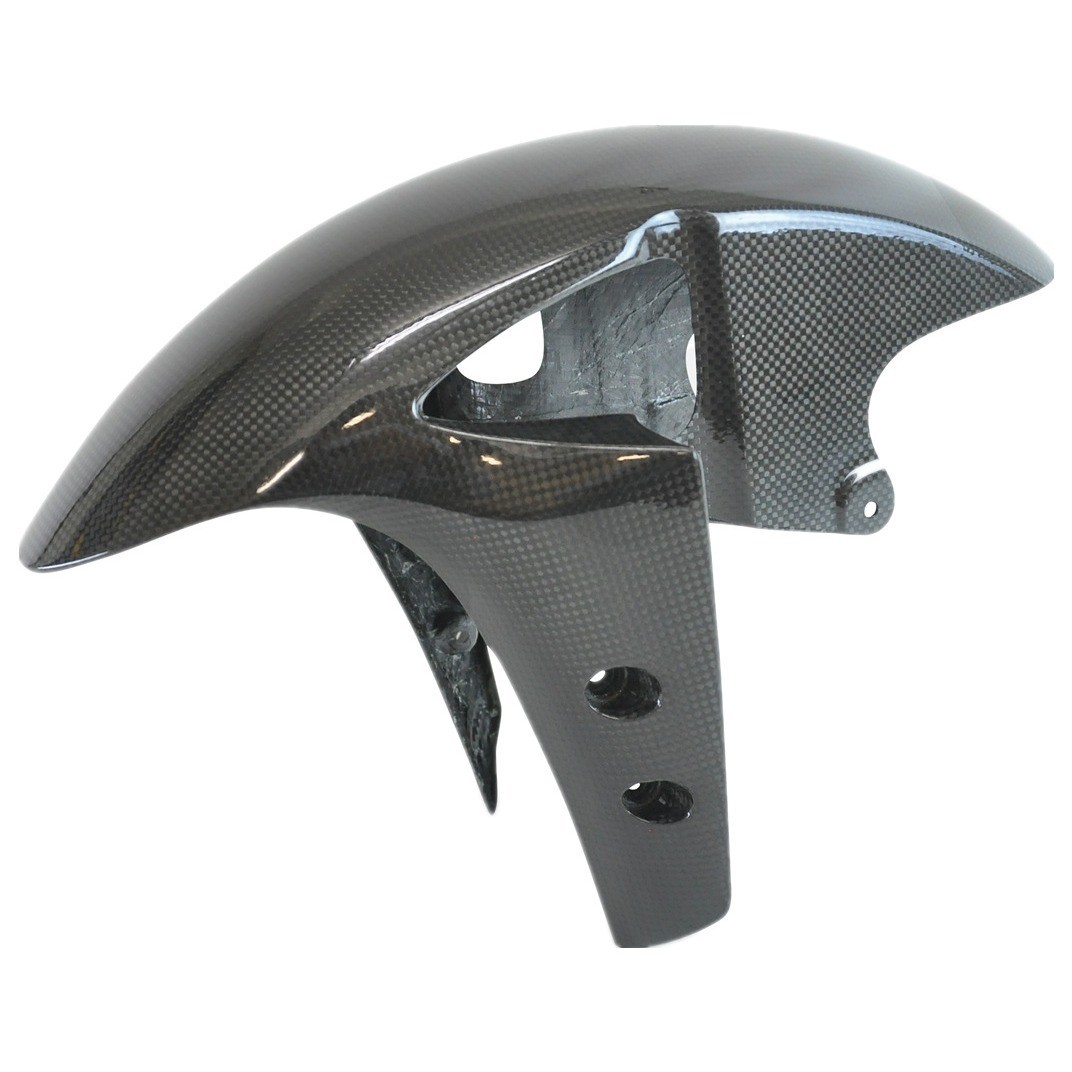
4. Dust Management
Extraction Systems:
Use high-efficiency particulate air (HEPA) filters to capture fine carbon fiber dust.
Ensure proper ventilation to protect operators from inhaling dust.
Personal Protective Equipment (PPE):
Operators should wear respirators, gloves, and protective clothing.
5. Post-Machining Finishing
Deburring:
Remove sharp edges or burrs using fine abrasives or manual tools.
Surface Finishing:
Apply clear coats or paints to protect the surface and enhance appearance.
Inspection:
Check for delamination, cracks, or surface defects using visual or non-destructive testing methods.
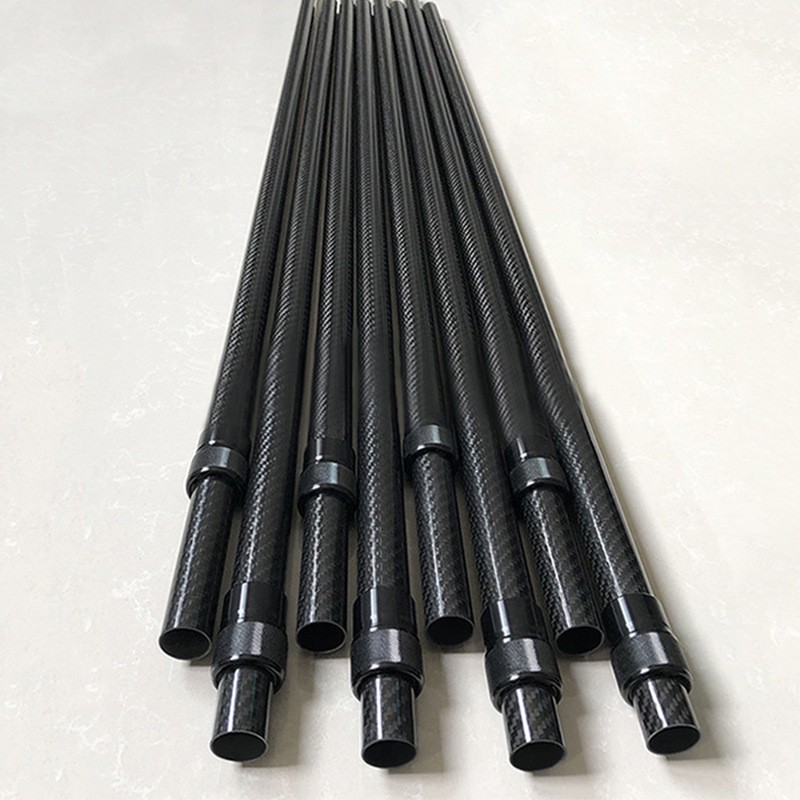
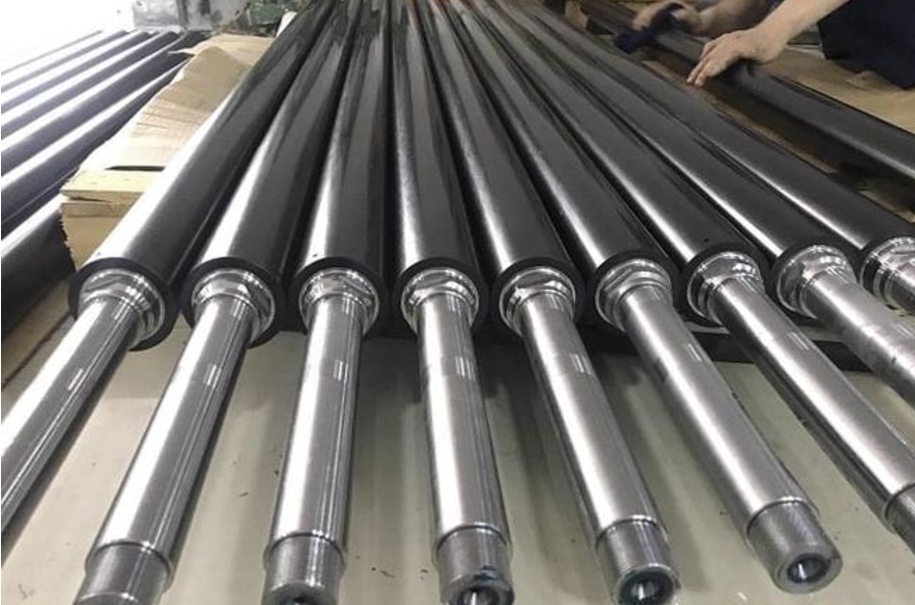
6. Applications of CNC Machined Carbon Fiber Parts
Aerospace: Precision components like brackets, mounts, and structural parts.
Automotive: Lightweight parts such as brake rotors, drive shafts, and body panels.
Robotics: High-strength, lightweight frames and arms.
Sports Equipment: Customized components for bicycles, drones, and racing gear.
7. Advantages of CNC Machining Carbon Fiber
Precision: CNC machining allows for tight tolerances and complex geometries.
Customization: Ideal for prototyping and low-volume production.
Material Efficiency: Minimal waste compared to traditional composite manufacturing methods.
8. Alternatives to CNC Machining
Near-Net-Shape Manufacturing:
Use processes like compression molding or resin transfer molding (RTM) to produce parts close to the final shape, reducing the need for extensive machining.
Waterjet Cutting:
Suitable for cutting flat carbon fiber sheets without generating dust.
9. Best Practices
Prototype Testing: Test machining parameters on scrap material before working on the final part.
Tool Maintenance: Regularly inspect and replace worn tools to maintain quality.
Operator Training: Ensure operators are trained in handling carbon fiber and CNC equipment.
By following these guidelines, carbon fiber parts can be successfully CNC machined to achieve high precision and quality while minimizing challenges like tool wear and delamination. Proper planning, tool selection, and dust management are critical to the process.